Introduction to Plunger metering pump
Metering pump is also called dosing pump, proportional pump and adjustable positive displacement pump.
It is a positive displacement reciprocating pump whose flow can be adjusted both dynamically and statically.
It is widely used in the production process of various corrosive and non corrosive liquid media that require accurate measurement, adjustable dosage and continuous proportioning.
Characteristic
The metering pump regulates the flow by changing the pump stroke and pump speed;
The metering pump can be adjusted arbitrarily from zero flow to rated flow, and the discharge flow is not affected by the discharge pressure; The metering pump can act as a pump, flowmeter and controller
Application
With the continuous development of China’s economy, the demand for metering pumps will be greatly improved.
Because metering pumps can meet the corrosion performance and sanitary requirements of transporting various chemicals, the amount of additives can be adjusted to achieve manual control and self-control, which is widely used and recognized by more and more industries.
At present, metering pumps are widely used in petroleum, chemical industry, oil refining, power, food, environmental protection, mining, water treatment, textile, plastic foam, paper making, medicine, national defense and scientific research institutes.
Classification
The metering pump can be divided into plunger metering pump and diaphragm metering pump according to the structure of hydraulic end.
Among them, the plunger metering pump can be divided into ordinary valved pump and valveless pump; Diaphragm metering pump is divided into mechanical diaphragm metering pump, hydraulic diaphragm metering pump and bellows metering pump.
Metering pumps are divided into electromagnetic driven metering pumps and motor driven metering pumps according to their driving forms.
In addition, there are metering pumps with hydraulic drive, pneumatic drive and other driving forms.
The metering pump with plunger (piston) as the element of linear reciprocating displacement in the working chamber is called plunger metering pump;
The metering pump with membrane elastic elements in the working chamber that cause periodic deflection deformation is called the hydraulic diaphragm metering pump (unless otherwise specified, the diaphragm metering pump refers to the hydraulic diaphragm metering pump);
The diaphragm of the mechanical diaphragm metering pump is connected to the plunger mechanism, and there is no hydraulic oil system.
The back-and-forth movement of the plunger directly drives the back-and-forth deflection of the diaphragm.
The structure of the corrugated pipe metering pump is similar to that of the mechanical diaphragm metering pump, except that the diaphragm is replaced by a corrugated pipe, and the end of the plunger is fixed with the corrugated pipe.
When the plunger moves reciprocally, the corrugated pipe is stretched and compressed, thus changing the volume of the hydraulic cylinder to achieve the purpose of infusion and metering.
Selection principle
- The metering pump is generally used for metering and transmission of media.
- Check whether the transmission medium is toxic, harmful, flammable and explosive. If yes, use diaphragm metering pump, otherwise use plunger metering pump.
3.The actual operating parameters should match the parameter table as much as possible, that is, the rated flow of the metering pump should be equal to or greater than the actual required flow, and the pressure must be less than or equal to the specified value of the parameter.
If it is too large, it will cause waste of the equipment. If it is too small, it is likely to cause damage to the equipment or reduce the life of the equipment.
- The best measuring accuracy range of plunger metering pump is 30% – 100%. The best metering accuracy range of diaphragm metering pump is 40% – 100%. If the requirements cannot be met within this range, special instructions are required
- After the metering pump model is determined, the materials of pump flow passage parts shall be selected according to the medium
Installation principle
The pump shall be installed on a workbench 50-100mm above the ground
The inner diameter of the inlet and outlet pipes shall not be less than the inner diameter of the pump inlet and outlet, and elbows shall be minimized to avoid “Ω” layout
The inlet pipe shall be equipped with a filter, and the outlet pipe shall be equipped with a safety overflow valve, pressure gauge, voltage stabilizer (accumulator)
The heavy load of the pipeline shall not be applied to the pump cylinder block
For suspensions and media prone to precipitation, the inlet and outlet pipelines shall be provided with tees
Pump control equipment shall be arranged near the pump working place as far as possible, and control switch protection equipment shall be added
Multi connected pump shall be from large to small according to the base, and the same base shall be from large to small according to the pressure
When installing the pump, pay attention that the center of the plunger metering pump is less than 2m above the liquid level, and the center of the diaphragm metering pump is less than 1m above the liquid level
When the liquid level is higher than the pump center, a back pressure valve should be added
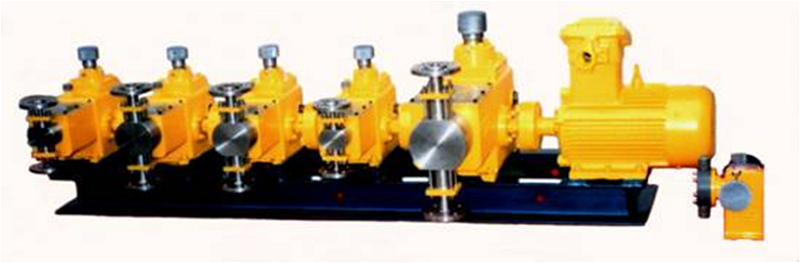
Maintenance of metering pump
- Pay attention to the readings of pressure gauge, ammeter and other instruments, and check whether the discharge pipeline is blocked or the valve is not fully opened when the pressure increases. If the current increases abnormally, check whether the pump and electrical equipment have problems
- Pay attention to whether there is any abnormal noise in the transmission parts and the operation of the pump valve.
- Check the leakage and temperature rise at the plunger. If the leakage is too much or the temperature rise is too high, adjust the packing gland
- The temperature rise of each pair and bearing shall not be too high, and the temperature of lubricating oil shall not exceed 60 ℃.
- All connections shall be free from oil and liquid leakage
- Regularly check the lubrication condition. The lubricating oil should be replaced in time. The new pump should be replaced every half a month. After two months, it should be replaced every half a year
- The oil in the diaphragm chamber should be replaced regularly. The new pump should be replaced once a week, once every half a year after 1-2 months of use, and once every half a year if it is used for more than 3 months